Preparing engineering data for a custom product can be a lengthy and complex process. It typically involves an engineer copying existing 3D CAD models and updating dimensions, suppressing and un-suppressing features, and replacing components to meet the client’s specifications. Once the 3D CAD models have been updated, the next step in the process is to create drawings, BOMs, and cut lists.
Design automation tools streamline this process by capturing and reusing design, process, manufacturing, and cost estimation knowledge to automatically create the documents and data required to sell and manufacture custom products.
Key Takeaways
1. Design automation tools automatically capture and re-use engineering design knowledge
2. Design automation streamlines the design of custom products
3. Businesses using design automation tools benefit from increased efficiency and productivity in their design and manufacturing processes
How Does Design Automation Work?
Capturing CAD Files
Capturing Engineering Knowledge
Specifying Product Requirements
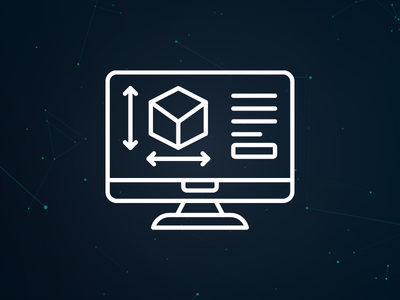
Design automation tools capture the parameters that would usually be manually updated by design engineers. Parameters are identified, named and saved in the design automation tools.
For example, the dimensions that control the size of a trailer chassis might be captured and named ‘Length’ and ‘Width’. And a structural member feature that is added if the trailer length is above a set size might be named ‘Extra Support’.
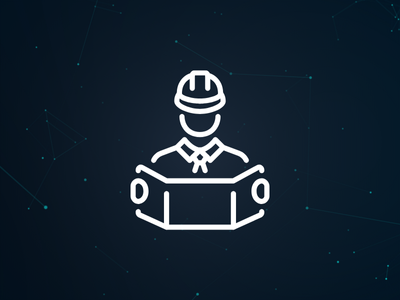
The next step is to capture the knowledge of the people who manually update the parameters in the CAD files, so the design automation tool can automatically make the updates.
DriveWorks captures the knowledge and actions of engineers using rules. DriveWorks rules can be equations, sums, business logic, legislation, and product requirements. They can be simple actions, complex calculations, or a series of instructions. Rules can also use information from databases, web services, and integrations with other company systems.
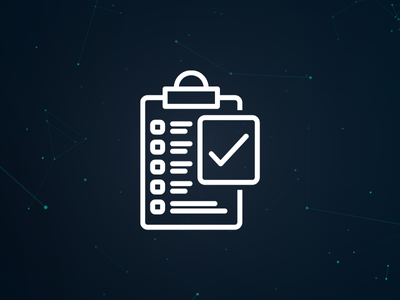
New configurations are specified by entering product requirements into a custom-designed User Interface (UI). The values entered are used in the rules to automatically update the 3D CAD files and create the manufacturing and sales documentation required.
Depending on your requirements and the design automation tool that you use, entering the product specification can be completed by the engineering team, internal sales team, distributors, or even the customer.
How Can Your Business Benefit From Using Design Automation?
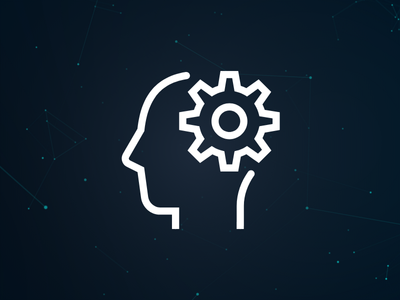
Solving the demand for skilled people
Recruitment and retention of skilled staff is an ongoing challenge for many businesses.
Design automation enables the knowledge and experience of your existing team to be captured and reused, making it easier for expertise and insight to be transferred to new team members.
By automating what are often repetitive, time-consuming tasks, existing team members are freed up to focus on more engaging tasks such as increasing throughput, solving custom design challenges, and improving existing products and processes.
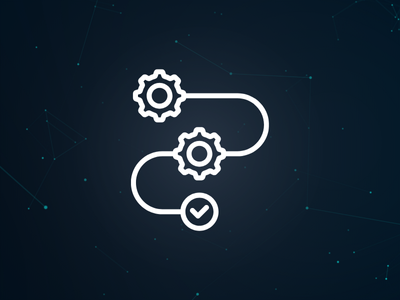
Streamlined Processes
Design automation is consistently accurate and significantly quicker than manually preparing files. Once a design automation solution is set up and has been tested, it will reliably output predictable results.
Combined with a custom UI that standardizes the input of values and ensures that the data entered is in the correct format, you can be confident that the files created will be accurate, consistent and meet the needs of the different teams using them.
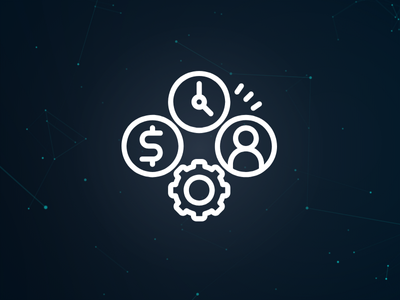
Free Up Engineering Resource
Quoting custom products typically requires engineering teams to prepare drawings for quote requests. This can place a lot of pressure on engineering resources.
Design automation enables engineering and design intent to be used by sales teams to quote custom products accurately, and automatically create approval drawings, BOMs, and associated sales and manufacturing documents.
Responding to quote enquiries quickly improves your quote to sale rates and enhances the overall customer experience.
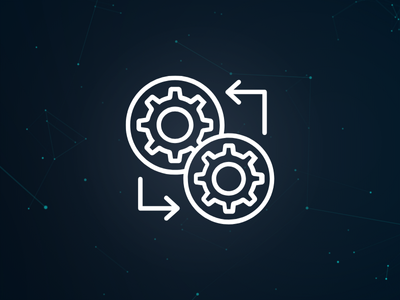
Integration With Other Company Systems
Configuring custom products and preparing the documents and data required by sales and manufacturing usually requires data to be shared and updated across various company systems.
Using a design automation tool that integrates with other company systems ensures that information used across your teams is always up to date. Automatically updating information in other company systems is faster and removes the risk of errors from manual data entry.
How Are Manufacturers Using DriveWorks Design Automation Software?
PL Custom Body use DriveWorks to automatically configure dimensions, custom properties and drawings
PL Custom Body are a custom vehicle manufacturer based in Manasquan, New Jersey. When they were tasked with getting their designs fully into SOLIDWORKS®, they wanted their engineers to focus on the specialized designs, not the commonly configured ones. They are now using DriveWorks to automate the configuration process of their custom ‘same but different’ ambulances.
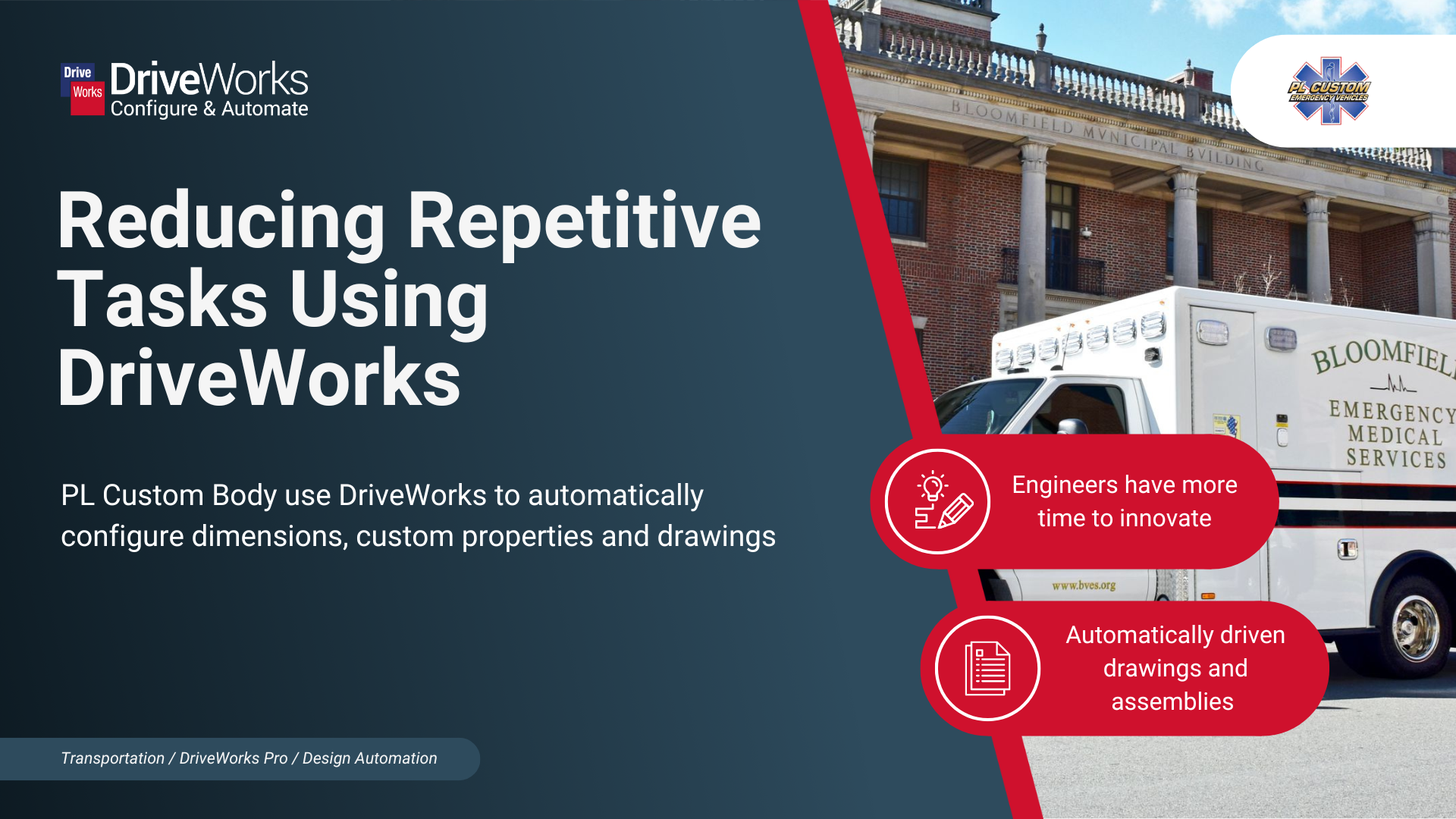
Learn More About Using DriveWorks for Automating Your SOLIDWORKS® Designs
Introduction to Using DriveWorks for Automating Your SOLIDWORKS® Designs Webinar
DriveWorks combines powerful SOLIDWORKS® part, assembly, and drawing automation with engaging 3D CPQ sales configurator features to enable manufacturers to implement a successful digital selling strategy, work smarter, reduce errors, and exceed customer expectations.
In this webinar, our product experts will share their knowledge and give you an introduction to Using DriveWorks for Automating Your SOLIDWORKS® Designs.
Learn how to capture and reuse design, manufacturing, and cost estimation knowledge to deliver custom products faster and with greater accuracy, without using complex macros, design tables or configurations.
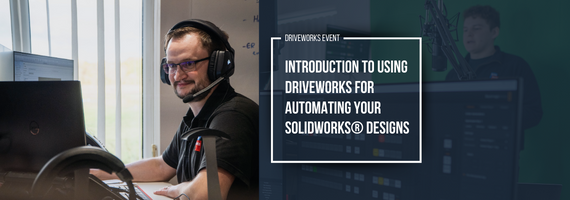