RJ Watson Inc. is based in Alden, NY and focuses on developing structural engineering solutions for the heavy construction industry world-wide. The company delivers a diverse and custom range of products and services including high load multi-rotational bearings, seismic isolation devices, expansion joint systems, noise mitigation materials, and FRP strengthening products for highway and bridge applications.
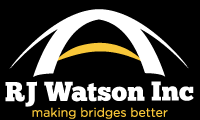
The Problem
Due to their Civil/Structural Engineering roots, the company had traditionally used 2D design applications for their engineering drawings. General 2D drawings are the requirement and have been the industry standard for decades. In 2013, RJ Watson recognized a potential opportunity to improve their process by leveraging the ability of parametric 3D modeling. Even though each of their bearing designs is custom and built based on application requirements, there is still consistency in the components. Each custom build is essentially a different configuration of something that has already been designed.
While reviewing RJ Watson’s process, CADimensions recognized the amount of effort spent toward fulfilling project proposal requirements. In order to be considered for a project, complete 2D product and general purpose drawings along with product specification data is required. Significant engineering resources were needed to fulfill these requirements even though they may not win the business to recoup that investment. This bottleneck hindered their ability to bid on all possible projects and increase the risk of missing deadlines on projects that they were pursuing.
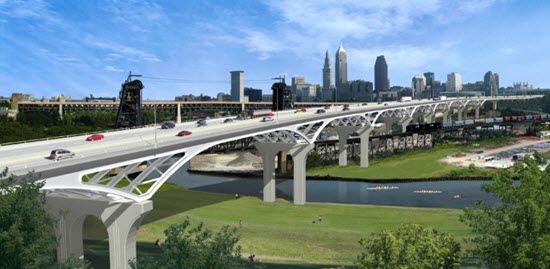
The Tools

RJ Watson invested in SOLIDWORKS to create their bridge bearing and product designs in 3D, and were able to automate the configuration of their assembly models and drawings based on specific bridge requirements with the use of DriveWorks. By implementing these tools, RJ Watson was able to reduce errors associated with product assembly and reduce the amount of time needed for fulfilling project proposal requirements by 50%.
By using DriveWorks to automate the process of creating drawings and elimating the need to adjust based on all custom builds, they were able to increase the number of new project bids, which they expect will yield more business for 2018. The overall process improvement will now support the future growth and goals for the company.
Summary
- Using the right tools to improve your processes saves you time in order to reach your project deadlines.
- DriveWorks helps automate your processes and eliminate time-consuming custom configuration.
- Using a parametric tool like SOLIDWORKS will directly impact growth and process efficiency.
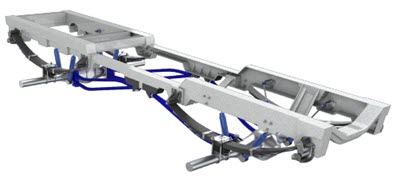