The food and beverage machinery manufacturing industry is highly competitive, with businesses under pressure to produce customized machinery that meets quality and environmental regulations.
Many manufacturers use design automation and CPQ solutions to streamline and optimize processes to maintain efficiency and reduce costs.
In this blog, we’re taking a deep-dive into the industry challenges and looking at how design automation and CPQ technology enables food and beverage machinery manufacturers to streamline processes and manufacture efficiently.
Customization requirements
In response to changing consumer preferences, food & beverage producers increasingly demand customized machinery solutions to meet specific customization requirements. Adapting equipment to different requirements without significantly increasing production costs or lead times is challenging.
Design automation enables manufacturers to easily adapt machinery to meet changing consumer demand. If a new trend emerges that requires different machinery parts, design automation solutions can quickly create variations based on pre-defined parameters. This level of flexibility enables speed to market, with the confidence of knowing that the machinery is viable and cost-effective.
Supply chain disruptions
Food and beverage machinery manufacturing is at risk of supply chain disruptions, leading to production delays, increased costs, and lost sales. Design automation enables agile machinery design changes.
In response to supply chain disruptions or material availability changes, manufacturers can quickly adapt machinery configurations without extensive manual reengineering, reducing the impact of disruptions and maintaining machinery supplier confidence.
Regulatory compliance
The food and beverage industry is subject to complex regulations, including food safety, nutrition and allergy labeling, packaging, and environmental laws. Ensuring compliance in production machinery is crucial, and balancing cost-effective machinery production while meeting regulatory requirements can be challenging. Keeping up to date with regulations also requires significant resources. Compliance can vary according to country and market, requiring multiple machinery variations depending on where products are manufactured and sold.
Design automation technology enables food and beverage machinery manufacturers to embed regulatory requirements into their design rules and workflows. This ensures that each piece of machinery complies with relevant regulations for food and beverage production. Machinery is configured to ensure it automatically complies with the latest regulatory standards. This reduces the risk of non-compliance and streamlines the process of adapting to changing regulations, ensuring that machinery always meets the current legislation.
Sustainability considerations
Food and beverage producers are increasingly looking for sustainable production options, such as reduced energy consumption and minimal waste. This requires food and beverage machinery manufacturers to produce machines that can efficiently deliver products and help in overall sustainability efforts.
Design automation solutions incorporate sustainability considerations into the design process, optimizing material usage and ensuring machinery designs comply with environmental standards and regulations. This helps food and drink manufacturers to achieve sustainability goals in their production processes.
Quality control
Ensuring the high quality and reliability of machinery is essential. Food and beverage producers rely on quality machinery to maintain efficient output and consistent production quality.
By automating the machinery design process, manufacturers enforce design standards and quality controls across all machinery designs. Consistent application of design rules and quality specifications ensures that machinery always meets quality standards. Consistent design quality promotes trust, reduces errors and rework and lowers production costs.
Using DriveWorks design automation solution for efficient croissant production
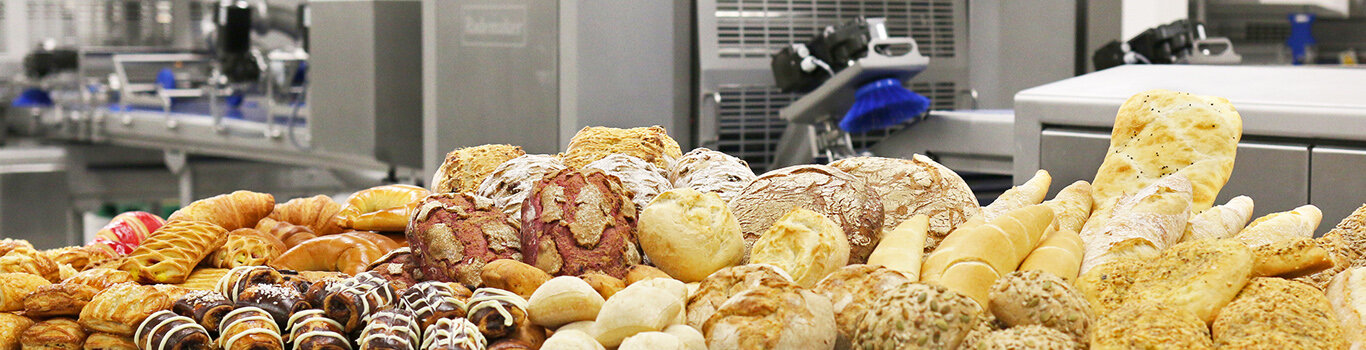
Rademaker has over 40 years of experience providing solutions for the food processing industry. Their broad portfolio of production lines includes bread, laminated dough, croissants, pastry, pies, and pizza.
Before implementing DriveWorks, the engineering time required to prepare an order for manufacturing was substantial and Rademaker identified the need for a product configurator and SOLIDWORKS automation solution to optimize their engineering processes. They wanted the ability to fill out the specification of a machine and have the 3D models, drawings, and BOMs automatically generated.
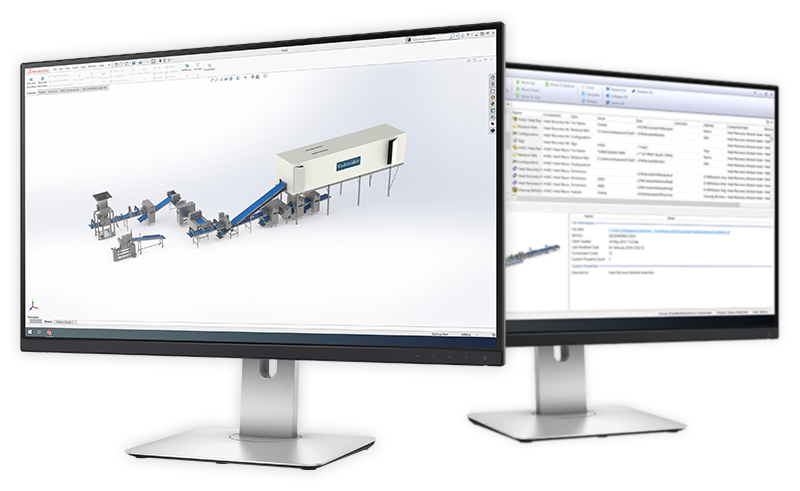
Using DriveWorks design automation technology, they now automatically update their SOLIDWORKS parts and assemblies, and create production-ready engineering drawings. This removes repetitive tasks from the engineering team, allocating valuable resources to other tasks.
With DriveWorks, Rademaker has achieved its target of reducing engineering time to less than 15 minutes for modular units. They also achieved a 30% reduction in time during the standardization process, using DriveWorks technology to optimize their product structure workflow.
DriveWorks is used by manufacturing companies from a range of industries. Because our technology is modular, scalable, and incredibly versatile, our customers use DriveWorks in many different ways, building design automation, product configurator, and CPQ solutions to suit their needs.
In our recent blog, How Different Industries Use DriveWorks, we looked in more detail at four of the many different industries where DriveWorks technology enables businesses to overcome their industry challenges.
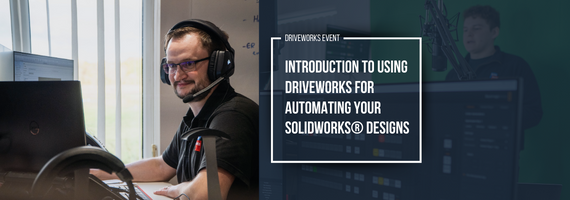
Introduction to Using DriveWorks for Automating your SOLIDWORKS® Designs
Tuesday, 8th April 2025 @3pm BST & 1pm AEST
In this live webinar, our product experts will share their knowledge and give you an introduction to using DriveWorks for automating your SOLIDWORKS® designs.
Learn how to capture and reuse design, manufacturing, and cost estimation knowledge to deliver custom products faster and with greater accuracy, without using complex macros, design tables or configurations.