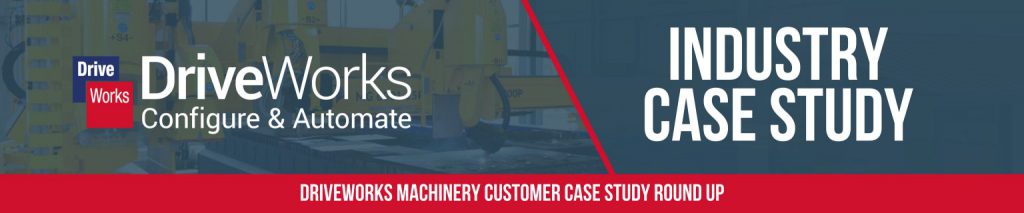
Manufacturers of machinery and materials handling products are using DriveWorks design automation & sales configurator software to improve manufacturing processes and be more efficient.
Machinery and materials handling products are often complex and require a significant amount of time to design and manufacture. The design process can involve customizations, a need for a high degree of precision, and the need to meet specific requirements. Because of this, design engineers and sales teams can spend a lot of time going back and forth over customer demands and capabilities. Design automation speeds up the design of custom products, cuts costs, and helps reduce errors. Combined with a CPQ configurator/ guided selling solution, orders are placed and manufactured even faster. It allows for seamless communication between all teams involved and a better customer experience.
Read on to learn how machinery and materials handling product manufacturers are improving processes and selling more with DriveWorks.
MicroStep
MicroStep, headquartered in Slovakia, is a renowned manufacturer of CNC cutting machines, tailor-made for industries around the world. With a large portfolio of products and a high volume of orders, it is not easy to deliver customized layout drawings for all the different kinds of machine quotes.
Before adding DriveWorks design automation software to their design process, the MicroStep design team would receive a basic hand-drawn sketch from a sales team member. The design team would then need to figure out exactly what the customer required based on the sketch given to them.
Adding DriveWorks to their quoting process has enabled MicroStep to build a configurator tool for their sales team. Using the DriveWorks configurator MicroStep’s sales team can guide a customer through the specification process, automatically selecting the parameters for their bespoke machine, such as the type and dimensions of material that the machine will cut.
During the sales process as each option on the form is selected, an interactive 3D preview of the machine is automatically displayed. This allows the customer to visualize their product’s appearance from different angles. The DriveWorks configurator also captures important customer information, such as name, email address, and shipping information.
When a MicroStep salesperson has completed the specification, a layout drawing is automatically generated, along with a summary document that details what the customer has ordered. These documents are then automatically sent to the customer for review. DriveWorks’ document generation capabilities mean all the desired files are automatically generated and named and ordered correctly.
Based on previous inputs, the configurator will automatically offer the recommended technology source for each bespoke machine. Inapplicable options on the form will become automatically disabled based on previous selections. This ensures that each specified machine is manufacturable and reduces costly errors in the manufacturing stage.
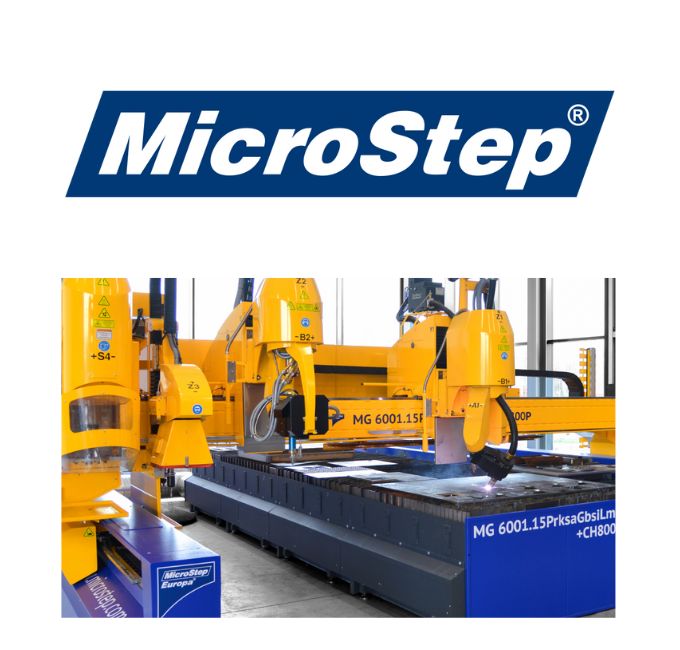
Learn more about how MicroStep are generating drawings in record time with DriveWorks Pro: How MicroStep Use DriveWorks
Rademaker
Rademaker has over 40 years of experience providing solutions for the food processing industry. Their broad portfolio of product lines includes bread, laminated dough, croissants, pastry, pies, and pizza.
Before using DriveWorks, the engineering time required to prepare an order for manufacturing was substantial. SOLIDWORKS models had to be manually updated to create the production drawings and bills of materials (BOM). Rademaker wanted to have the ability to fill out the specification of a machine and have the 3D models, drawings, and BOMs automatically generated.
Using DriveWorks, their product specifications are used to automatically update the SOLIDWORKS parts and assemblies and create production-ready engineering drawings. This removes repetitive tasks from the engineering team, freeing up valuable resources for other tasks.
Modular implementation of DriveWorks has allowed Rademaker to reuse projects, driving standardization and improving engineering efficiency.
Rademaker also integrated DriveWorks with their existing SAP-PLM solution, facilitating the process of standardization, change control, logistics, and sales.
Now, Rademaker has achieved a 30% reduction in time during the standardization process, optimizing their way of working with product structures. They have increased flexibility, variants, functionality, and the number of options they can handle. Because of this, Rademaker has achieved their target of reducing their engineering time to less than 15 minutes for modular units.
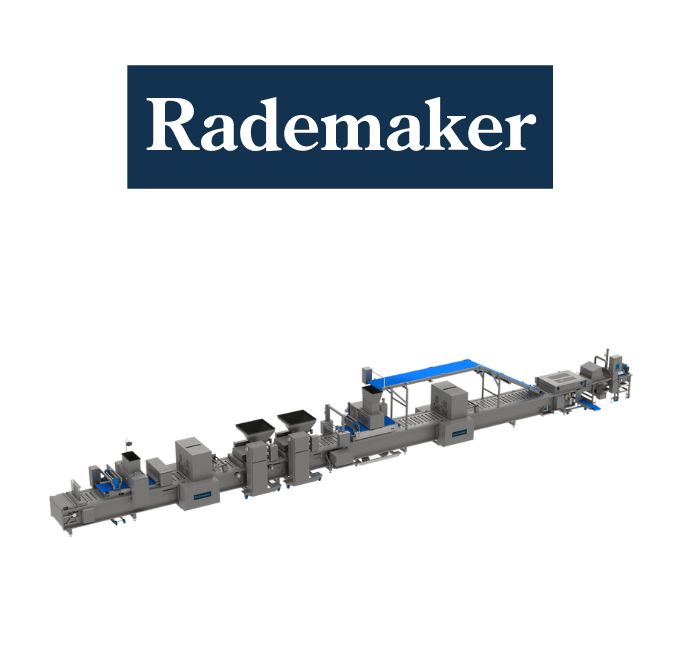
Learn more about how Rademaker are reducing engineering time with DriveWorks Pro:
IMA PG
IMA PG is a leading pioneer in packaging solutions in India. Operating in the pharmaceutical industry, they’ve been designing and manufacturing machinery for various pharmaceutical products and tablets since 1961.
Before DriveWorks, IMA’s design-to-manufacture process required an engineer to design every part component by changing each dimension manually. They also had to give annotations and dimensions for every view in a drawing sheet. With so much manual input, the risk of costly human error in the design process was high.
Introducing DriveWorks has revolutionized the way IMA designs its products. They have now configured DriveWorks for layout and component designing. This means an engineer can now input the requirements for each specification into their form. Once the form is completed, the new model along with its manufacturing data is automatically generated and ready to be sent to the manufacturing floor.
Using DriveWorks, IMA can respond to sales inquiries much faster, reducing their lead time significantly, and opening up even more sales opportunities.
They have particularly benefitted from DriveWorks in the Cavity Die part of their design process. The cavities are changed depending on each specification, for example, they might be round, or oblong. This process is now specified and controlled through DriveWorks, and the plate size is driven through variable parameters.
DriveWorks has played a crucial role in IMA’s day-to-day work, helping them to achieve two important goals: savings and accuracy.
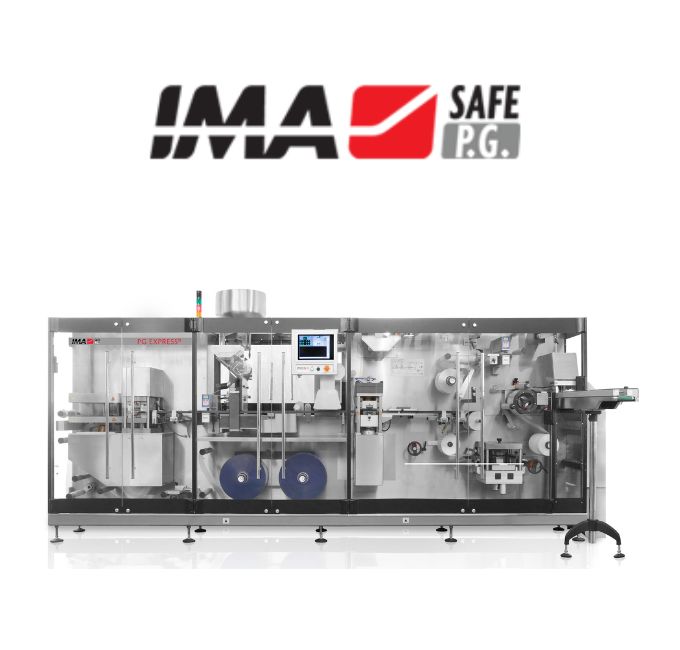
Learn more about how IMA PG have sped up their design process and reduced costly errors with DriveWorks Pro: How IMA PG Use DriveWorks
Explore our DriveWorks Configurator examples, and see different examples of how DriveWorks can be used for design automation and digital selling.
Our scissor lift configurator example is just one example of what’s possible with DriveWorks. Explore and interact with this and other examples at DriveWorksLive.com
Try DriveWorks Solo for free
Get instant access to DriveWorks Solo for 30 days. No credit card required.