Manufacturing for the architectural and building components industry means dealing with complex, custom designs every day. Additionally, manufacturers face the challenges of staying competitive, following strict regulations, and ensuring design quality and consistency.
In this blog, we take an in-depth look at the challenges faced by architectural and building components manufacturers and explain how DriveWorks design automation, 3D product configurator, and CPQ technology are used by manufacturers to overcome those challenges.
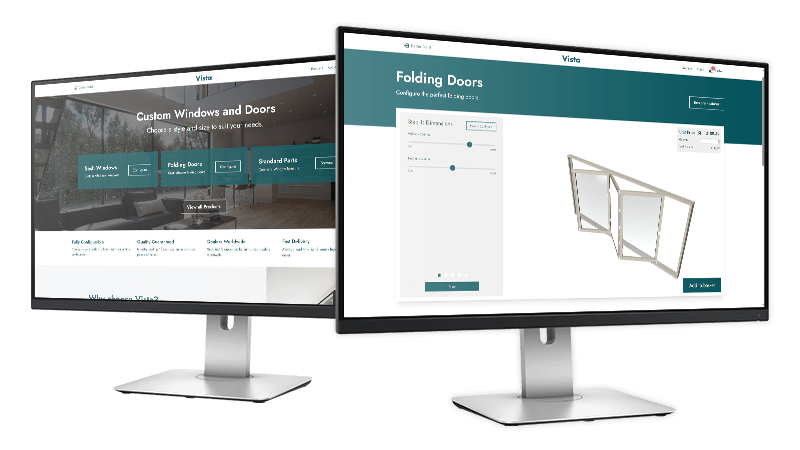
Customization
Architectural and building components often need to be highly customized to meet the specific design requirements of different projects. This level of customization is challenging and involves a large amount of manual input from a design, quoting, and manufacturing point of view. This results in complicated workflows, production inefficiencies, and costly errors and rework.
DriveWorks technology enables architectural and building components manufacturers to quickly and accurately create custom designs. Using pre-defined rules and parameters that incorporate design feasibility constraints for materials and manufacturing, custom designs are automatically generated. This ensures that each custom order, no matter how complex, follows a standardized and automated design process. Design times are reduced, and design engineers are freed up to spend more time on other work, such as new product development.
Material costs and availability
The cost and availability of materials impact production costs, profit margins, and design accuracy.
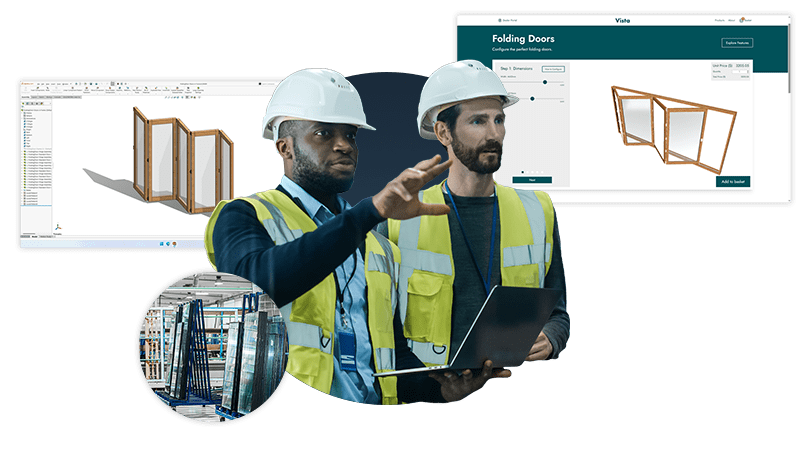
DriveWorks technology enables agile design changes to accommodate material changes, and pricing is automatically updated to reflect current costs. This enables manufacturers to easily adapt to changing market conditions and to ensure design and production continuity.
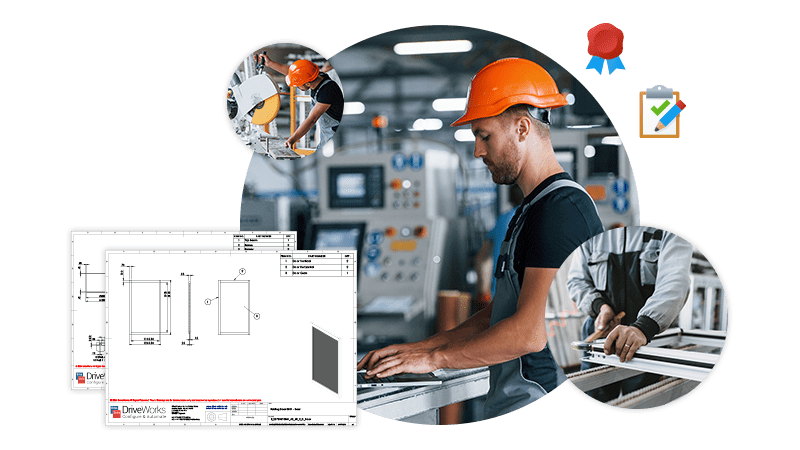
Quality control
Manufacturing custom architectural and building components that consistently adhere to quality standards is key for business success. Quality control requirements can be complex, making it challenging to confidently and consistently meet quality standards for all custom orders.
DriveWorks ensures consistency in design by using standardized rules and parameters. This reduces the risk of errors, ensuring that products consistently meet quality standards, and improves customer satisfaction.
Regulatory compliance
The architectural and building components industry is subject to a wide range of different building codes and regulations. Regulations can also vary by country, presenting a particular challenge for manufacturers who sell globally. Ensuring that all products comply with relevant regulatory standards is critical, and failing to meet regulatory requirements can result in fines and product recalls.
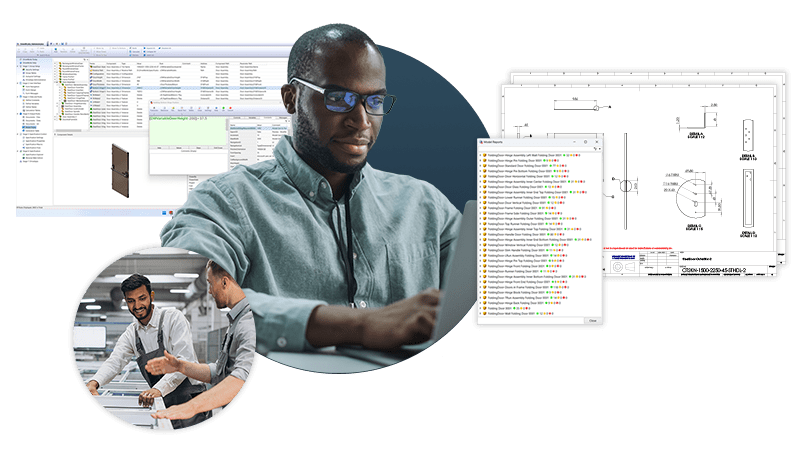
DriveWorks enables manufacturers to embed regulatory requirements into design rules, ensuring every custom product is compliant. This is key for business reputation and customer satisfaction. It also ensures that costly design errors are avoided.
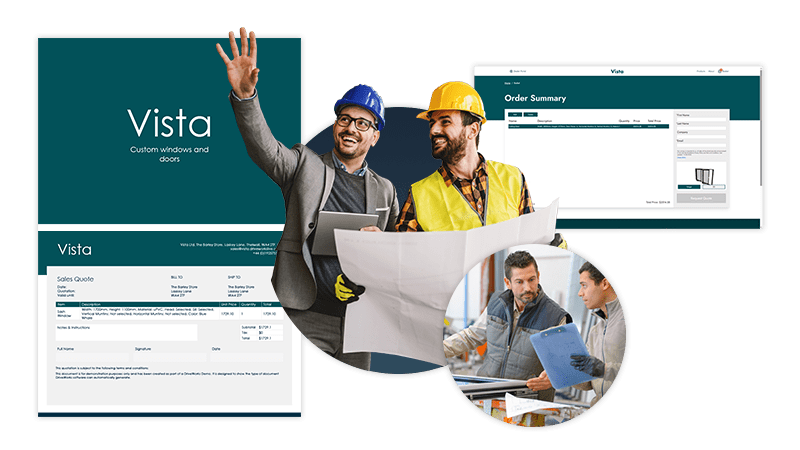
Long sales cycles
The sales cycle in the architectural and building components industry can be lengthy, especially for large-scale projects. This can impact project timelines and revenue flow.
DriveWorks technology automates design and quoting processes, enabling manufacturers to respond quickly to customer inquiries and reduce the length of time it takes to finalize orders. This efficiency is important for projects where delivery time is a critical factor.
Meeting door customization requirements with DriveWorks
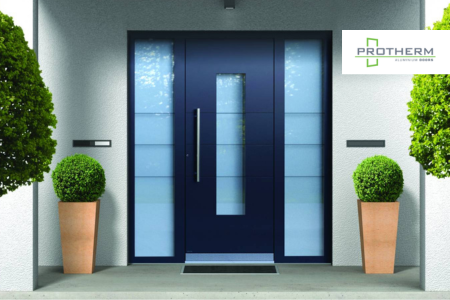
Protherm, based in Slovenia, develops, manufactures, and sells aluminium doors for houses and commercial buildings. Due to the large number of design choices and possible configurations, Protherm had an urgent need for a configurator to simplify its processes. Protherm needed a solution with the flexibility to configure unlimited options, user-friendly tools, and the ability to show real-time images.
Protherm’s implementation uses the DriveWorks CPQ DriveApp. This supplied them with a range of project templates, which they could then customize to meet their needs. Alongside the default projects, Protherm have added two additional projects, one for viewing documents and the other for monitoring production.
With over 2000 variations possible, it is vital Protherm’s configurator can limit design choices, based on rules, to ensure all configurations are manufacturable. Users can then select their required model, colors, accessories, and more to ensure their door meets their requirements. The prebuilt projects help to speed up implementation. Project rules and permissions are already built in, so Protherm could start adding their own users quickly while maintaining control over their order process.
The custom Documents project that Protherm has added to their implementation enables users to review their documents and see the revision history, helping to reduce errors and ensure consistent quality. Real time images are displayed as each door is configured. With previous systems, it took up to 24 hours to create an image to communicate the configured design to the user, this is now shown instantly in DriveWorks.
“With DriveWorks, we have created a really easy to use tool, with a simple interface, that allows you to quickly choose what you want from many options.”
Dragan Nik Lukes, DriveWorks Engineer for Protherm
Configure, design, sell, and manufacture architectural and building components faster
DriveWorks technology enables you to accurately configure custom products, calculate pricing, and automatically create documents and data for sales and manufacturing.
Learn more about DriveWorks technology and how your business could benefit with a DriveWorks demo. One of our technical experts will be able to take you under the hood of our technology and explain the features of our design automation, product configurator, and CPQ for manufacturing solutions in more detail.