
How Can Manufacturers Do More With Less?
Digital transformation is the integration of digital technologies to create new, or modify existing, processes within an organization. Adopting digital technologies is enabling companies to increase efficiency, improve accuracy, streamline business-to-consumer relations, boost speed, and innovate.
Digital technologies are helping businesses to stay ahead of their competition and improve traditional processes. Technology is driving the manufacturing industry forward and helping organizations to succeed.
Knowing and understanding the possibilities of what digital technologies can do to simplify processes is key to understanding how you can do more with less. Less time time spent on monotonous tasks, means a more productive workforce. Simplifying processes means more opportunities for business growth. Digital technologies open doors and enable businesses to do more with lower costs and fewer resources.
Technology has the power and capability to reduce the challenges that businesses face today, enabling businesses to optimize processes and save money without having to invest in expensive initiatives or resources.
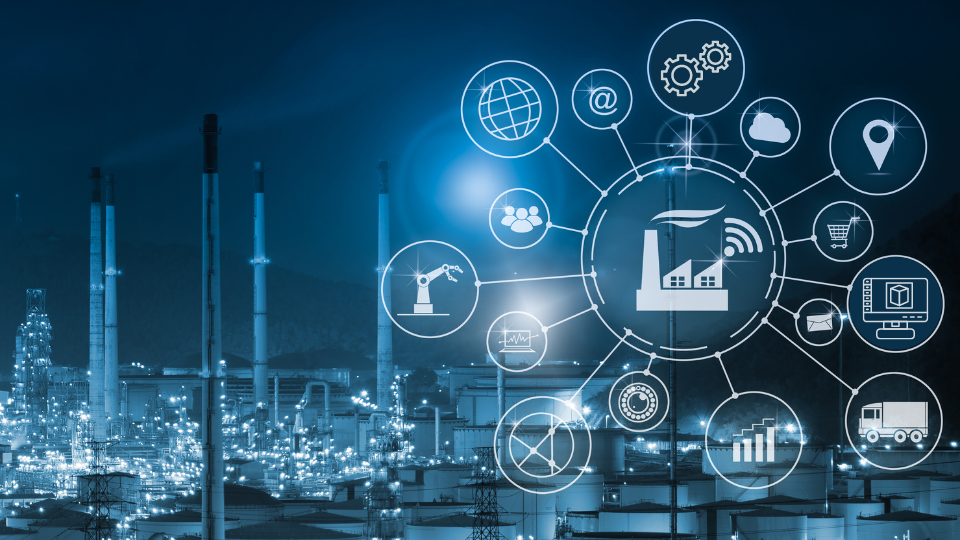
Why are Digital Technologies Beneficial for Manufacturing Businesses?
The benefits of digital technologies can reach all corners of a business. Digital is improving communication and promoting collaboration. Digital-focused companies are more agile, enabling growth. These benefits are resulting in increased efficiency, more productive workforces, and improved customer experiences.
Automating and digitizing internal business processes increases productivity and improves customer experiences. Teams who collaborate effectively are more productive. They have more time for creativity and adding value.
Digital processes make it easier for organizations to anticipate and adapt to changes. It also provides better planning opportunities, implementing and nurturing new strategies.
In the current climate, companies are looking for ways to do more with less, and technology is helping to do just that. Digital transformation results in fewer errors, a more productive workforce, reduced overhead costs, and more opportunities to make improvements. It allows mundane tasks to be automated, speeding up processes and increasing throughput.
What Doing More with Less Means for Manufacturers
Factors like rising costs, increasing customer demand, and more specific consumer needs mean that organizations need to find ways to meet expectations whilst accelerating productivity, being as efficient as possible and maintaining quality and service. Doing more with less using the power of technology is helping manufacturers to;
- Save on costs
- Increase productivity & efficiency
- Accelerate company agility
- Increase stakeholder engagement
The adoption of technology is becoming crucial to overcoming bottlenecks within business processes, staying ahead of competitors, and securing long-term growth.
Reducing Costs & Starting Small
There is a growing global commitment to embracing digital technologies. Businesses around the world are expected to spend $2.8 trillion on digital transformation, twice as much spent in 2020. While the prospect of implementing technologies can seem daunting, especially to those who haven’t yet, it’s important to remember you don’t have to make big changes all at once. Digital transformation is scalable. Sometimes, with what feels like a ‘big problem’, it can be easy to assume it needs a big solution, requiring a lot of time, money, and change. This doesn’t need to be the case.
Taking advantage of opportunities to try free trials, ROI calculators can not only kick-start initiatives within a business but allow companies to begin reaping the benefits of technologies before committing to a cost. Whilst there is an initial cost to investing in digital technologies, they can help reduce costs in the long run and companies are quickly seeing a good return on investment. 56% of CEOs say digital improvements have led to increased revenue.
Businesses can also reduce initial set up cost by utilising tools and software they already have. What technologies do you already have in your business? Are you using them to their full potential? Are there features and functionality you’re not using? Does one team use a digital tool that would also be useful for another team?
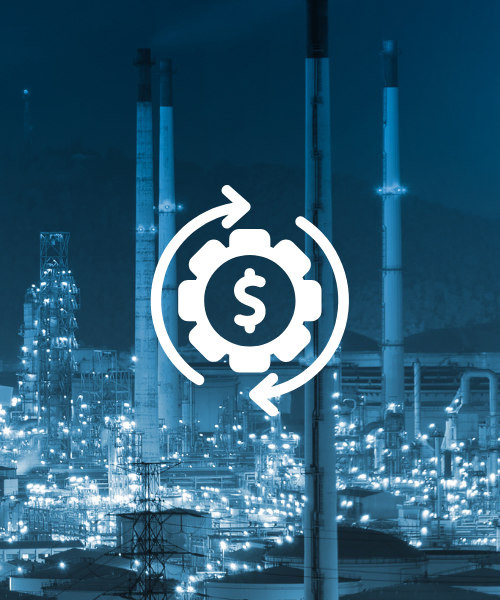
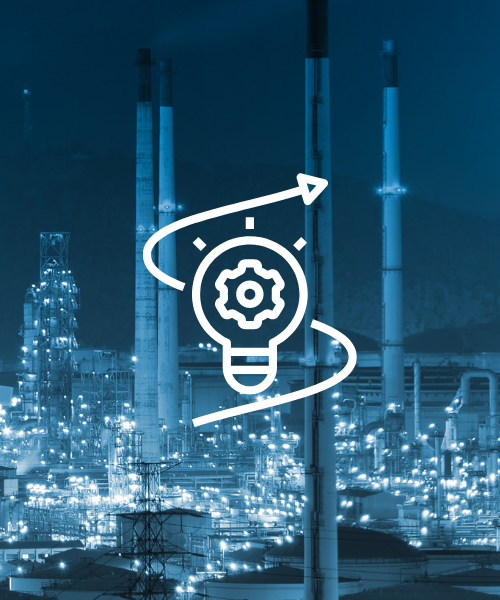
More Efficiency & Fewer Errors
Automating business processes creates a more effective and efficient workforce. Valuable time saved can be used to innovate more and add value. Automation can help you:
- Make data-driven decisions
- Reduce errors
- Standardise
- Promote communication between teams
- Save time
Through automation, complex business processes are being made smarter. Business Process Automation is enabling businesses to become more streamlined. Automation uses information and data to manage routine processes, reduce errors and costs, increase productivity, and improve efficiency.
By automating time-sensitive and often repetitive activities, businesses can do more with less, improving throughput and quality to meet customers’ requirements. Automation is freeing up engineers, enabling them to get through more orders in less time, and reducing costs and errors. Sales teams are becoming more proficient meaning customer inquiries are being dealt with faster and with better detail. Automation is leading to more orders, reduced operational overheads, and better customer service one step at a time.
Be More Agile & Stay Ahead
Businesses without a strong digital strategy are likely to struggle to be as agile as their competitors. Digitally-savvy companies are able to move faster to adapt to rapid changes in the market. They are able to embrace new opportunities quicker and see benefits sooner.
Implementing digital technologies into the manufacturing process can improve an organization’s agility, as they can be more responsive to meeting customer needs and have flexibility on product lines.
Digital processes make it easier for organizations to anticipate and adapt to changes. It also provides better planning opportunities, implementing and nurturing new strategies.
Organizations couldn’t have predicted or prepared for the covid-19 pandemic. However, those who had already embraced digital technologies were quicker to adapt. They were able to operate during difficult times and were able to survive. The pandemic encouraged more companies to use digital technologies. The benefits achieved inspired them to continue with their digital journey afterward too. 86% of companies that implemented digital technologies as a result of the pandemic will continue to accelerate their adoption of digital.
In the current climate, companies are looking for ways to do more with less. An increasing skills gap makes it harder for companies to hire. Increasing business costs also means companies cannot always increase their recruitment budget. These challenges shouldn’t restrict growth – digital technologies are key to increasing agility to get the most from existing resources and people.
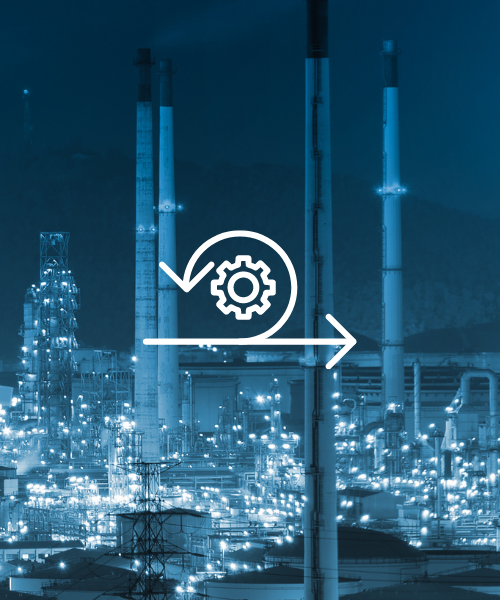
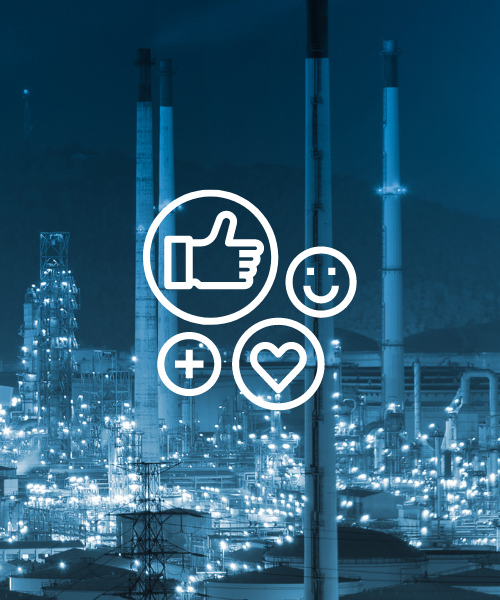
Improve Employee Engagement & Retention
Investment in technology shows a commitment to investment in the future of a company. This has positive effects on stakeholders like employees. All teams can feel the benefits of digital transformation. Automating mundane, repetitive tasks and reducing errors improves job satisfaction. Using digital technologies frees up employees to be more productive, and focus on what humans do best – adding value. From sales and engineering, all the way to HR, there will be opportunities to streamline processes. This will change the way your business operates and improve customer experiences too.
This promoted reliability can not only create more opportunities for your market, but it can also create opportunities for internal areas of businesses to thrive. This could be in the form of employees highlighting ways other processes could benefit, or finding technologies themselves after being inspired.
The benefits are also passed on to customers – with faster order and delivery processes and more accurate end products. Better customer satisfaction results in more orders and more customer loyalty, retention, and recommendations. Improving sales processes improves customer experiences, builds customer loyalty, and increases sales. Resulting in more motivated sales teams and driving revenue for the organization. Technology helps to meet the growing need for the fast-on-demand creation of products from customers.
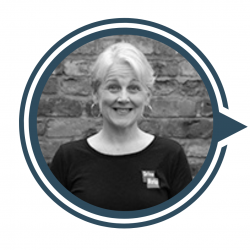
Heather Hasz
Brand & Community Ambassador, DriveWorks
“I’ve seen for myself how companies that have adopted digital technologies to do things like automate their designs have seen a drastic reduction in design times and can get to market quicker.
At DriveWorks, we’ve seen customers do more with less by creating a full 3D configurator and now offer ‘guided selling’.
They can devote more time to other areas of their business.”
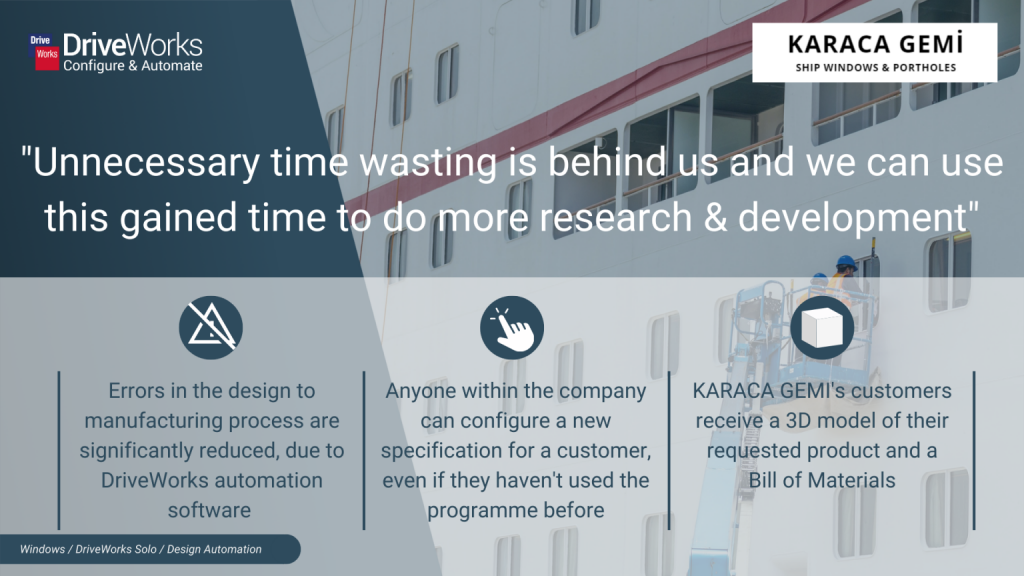
KARACA GEMI, based in Turkey, design and develop specialised glass for a range of ships around the world.
Since implementing DriveWorks Solo in June 2021, KARACA GEMI have achieved a number of goals:
- Reducing the time taken to create 3D drawings of specified parts
- Automatically generating accurate and relevant documents
- Reducing the number of errors during the manufacturing process
- Their customer inquiry response time is faster and there are fewer errors in the design to manufacturing process.
- DriveWorks’ document generation capabilities means all the desired files are automatically generated and named and ordered correctly.
- They can guide the customer through the product options on the configurator, and submit an accurate order straight to the design team.
Find out more about how KARACA GEMI are automating with DriveWorks here.