Integrating design automation into your design process enables your teams to work smarter, making your business more flexible, efficient and, competitive. Regardless of your business size or the sector that you work in, design automation can give you a significant competitive advantage.
DriveWorks is used by manufacturing companies from a range of industries. Because our technology is modular, scalable, and incredibly versatile, our customers use DriveWorks in many different ways, building design automation solutions to suit the needs of their own businesses.
Seeing how other companies use DriveWorks is a great way of understanding how our technology works. It enables you to see how manufacturers have adopted our technology across a range of different industries and the benefits they’ve achieved with design automation. Seeing real-world examples and business metrics enables you to think about how you could incorporate design automation technology into your processes, and the efficiencies you could benefit from.
In this blog, we’re sharing 5 DriveWorks design automation customer success stories.
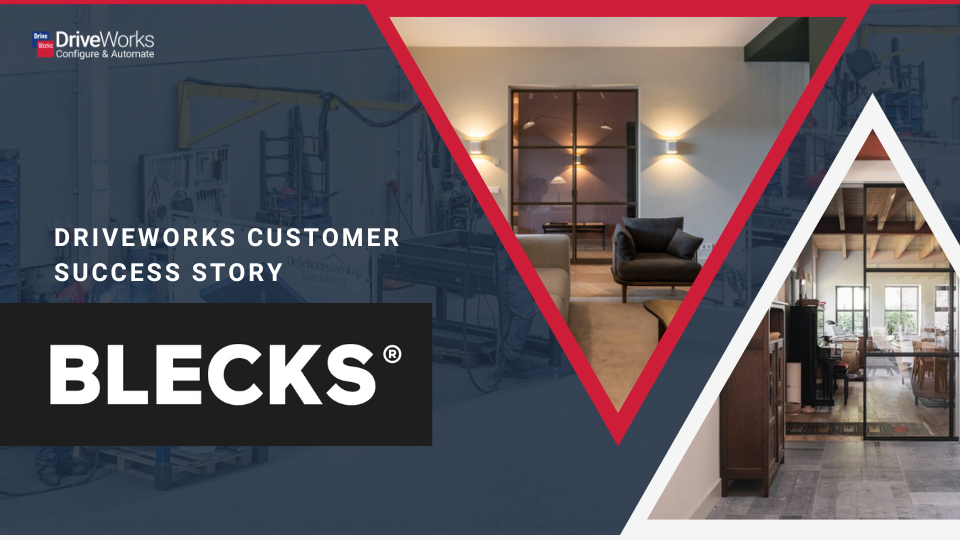
Blecks: Speeding up workflows and automating repetitive tasks
Blecks, a Netherlands-based manufacturer of chimney caps, steel doors, and steel stairs, had a significant amount of manual workload in their design process. To meet growing demand for their products they needed a solution to speed up their workflow and automate repetitive tasks. To help with this, they began using DriveWorks Solo to streamline their operations.
After seeing the value of DriveWorks, they then scaled up to DriveWorks Pro to take their design automation to the next level and incorporate a configurator solution for their steel door product line.
Blecks have automated the cutting of parts for their chimney caps using DriveWorks. DriveWorks drives the generation of 2D drawings, part lists, and .dxf files for laser cutting. Information is passed into SOLIDWORKS® custom properties which is then etched onto each part to help identify it after cutting. The chimney caps now have a design automation rate of 95%, with over 900 orders having been run with DriveWorks.
Würth: Embracing design automation
The Würth Group is the global market leader for assembly and fastening materials. Central to their success is Adolf Würth GmbH & Co. KG, the largest company in the Würth Group, based in Künzelsau, Germany.
They use DriveWorks to revolutionize their product customization, specifically focusing on their extensive wood screw range.
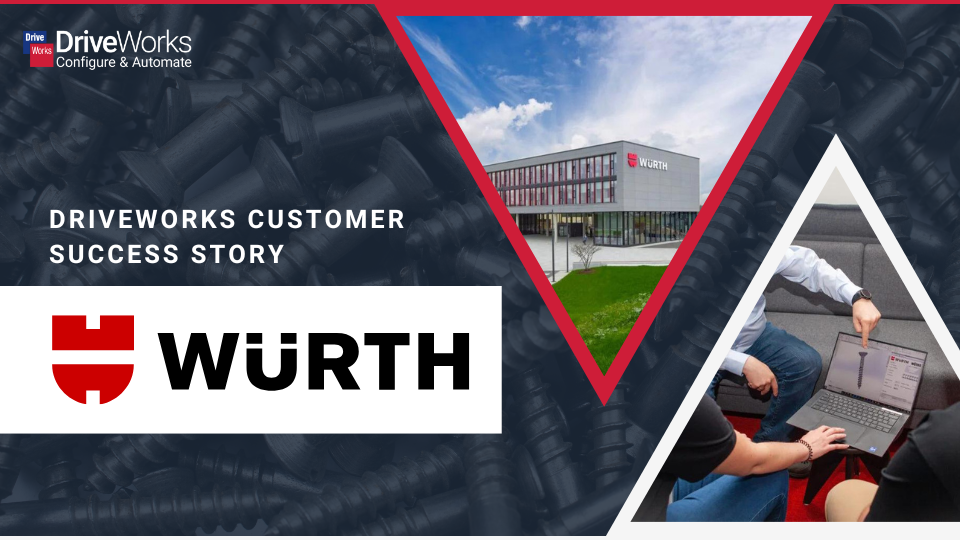
By integrating DriveWorks with SOLIDWORKS, Würth developed a product configurator for their wood screws. The configurator automates the creation of custom wood screw models, drastically reducing the time and effort involved. There are over 1,400 possible configurations of the screw, with parameters including; head shape, thread geometry, and milling elements.
The implementation of DriveWorks has delivered several benefits for Würth:
- Efficiency: The automation of custom model creation has significantly reduced the time required to produce each variant. What once took hours now takes minutes, freeing up design engineers to focus on more complex tasks.
- Accuracy: Manual creation of CAD files was prone to errors. With DriveWorks, the risk of human error is minimized, ensuring each model is accurate and meets the specified requirements.
- Ease of use: DriveWorks’ rules-based technology is user-friendly and does not require programming knowledge. This ease of setup enabled Würth to quickly implement the configurator and train new users efficiently.
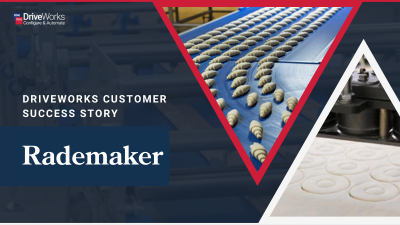
Rademaker: Reduced engineering time and increased quality
Rademaker has over 40 years of experience providing solutions for the food processing industry. Their broad portfolio of production lines includes bread, laminated dough, croissants, pastry, pies, and pizza.
Before implementing DriveWorks the engineering time required to prepare an order for manufacturing was substantial and Rademaker identified the need for a product configurator and SOLIDWORKS automation solution to optimize their engineering processes. They wanted the ability to fill out the specification of a machine and have the 3D models, drawings, and BOMs automatically generated.
Using DriveWorks technology they now automatically update their SOLIDWORKS parts and assemblies, and create production-ready engineering drawings. This removes repetitive tasks from the engineering team, freeing valuable resources for other tasks.
Subsequently, Rademaker achieved their target of reducing engineering time to less than 15 minutes for modular units. They also achieved a 30% reduction in time during the standardization process as DriveWorks enabled them to optimize their product structure workflow.
Wozair: Working smarter and staying ahead of the competition
Wozair Limited is based in the South of England and specializes in the design and manufacture of high integrity heating, ventilating, and air conditioning (HVAC) equipment for the Renewables sector.
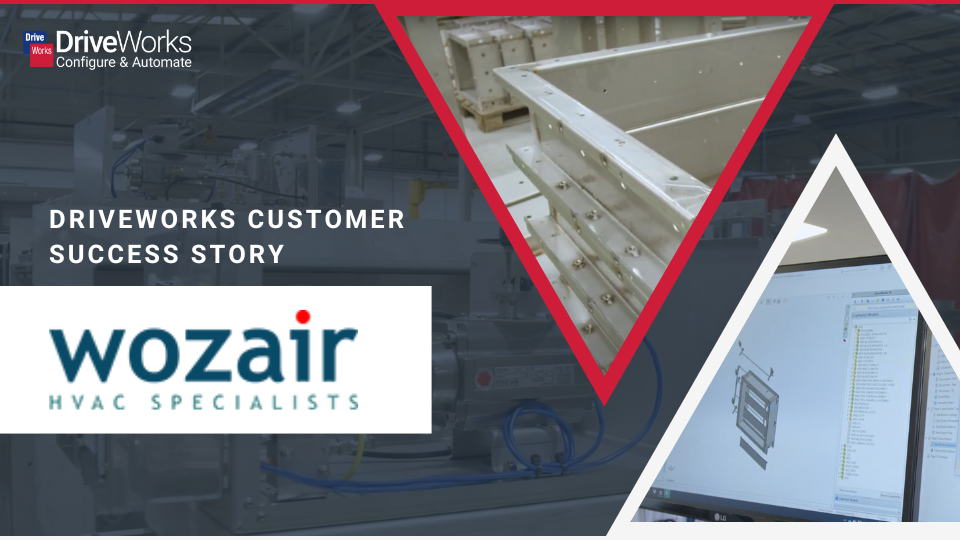
Implementing DriveWorks has enabled Wozair to automate and streamline their design process, reduce their risk of human errors, and improve communication between their design and manufacturing teams. They’ve also been able to gain additional accreditations, ensure material traceability, and harness the expertise and knowledge of their design engineers.
Before using DriveWorks, Wozair relied on an outdated Excel-based Integrated Design System to produce their .dxf and BOM files. Implementing DriveWorks has led to a reduction in the number of manual inputs required and allows them to get the design information through to manufacturing in a shorter space of time.
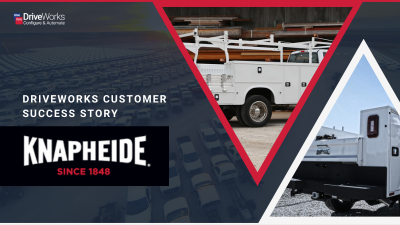
Knapheide: Automating mundane tasks and meeting demand
Based in Illinois, USA, Knapheide is a truck body manufacturer with a family-run history that spans over 175 years. They are committed to supplying a diverse product offering and encouraging customization.
Before implementing DriveWorks, engineers at Knapheide worked on a lot of mundane tasks in design work, drawings, creating BOMs, adding notes, dimensions, and tens of thousands of parts throughout product iterations. They weren’t able to create 3D models for all of their products because they couldn’t keep up with the volume.
DriveWorks has enabled Knapheide to automate mundane tasks so that designers can focus on the fun part – the design cycle. DriveWorks has opened a communication bridge between designers and those on the shop floor. Knapheide’s engineers can now provide detailed 3D models directly to the shop floor. They are more efficient and able to keep up with the demand they struggled to meet before implementing DriveWorks.
How can I implement design automation in my business?
Implementing design automation into your business shouldn’t be daunting. Starting small and quickly seeing the benefits is an effective way of introducing design automation technology into your processes. In a recent blog, we shared our tips for design automation implementation showing how easy it can be to start your design automation journey.