Digital Transformation
The term Digital Transformation has attracted a lot of attention across the manufacturing industry and throughout the media recently. Defined by The Enterprisers Project, Digital Transformation is “the integration of digital technology into all areas of a business, resulting in fundamental changes to how businesses operate and how they deliver value to customers.”
With digitalisation comes the rise of trends such as Industry 4.0, smart manufacturing and smart factories. Industry 4.0 refers to the ‘Fourth Industrial Revolution’, the next step where manufacturing moves away from a physical world and towards a digital one.
The industry has been continually evolving since the first Industrial Revolution in the 1700s. Past industrial revolutions have shown what can be achieved when an industry is transformed.
This fourth industrial revolution is all about focusing on connectivity and communication.
A future where the production process is being completely restructured to be streamlined and agile.
In this fourth revolution, devices are connected, they can communicate, and they can make smart decisions. Data and analysis is key to making informed decisions and improving efficiencies.
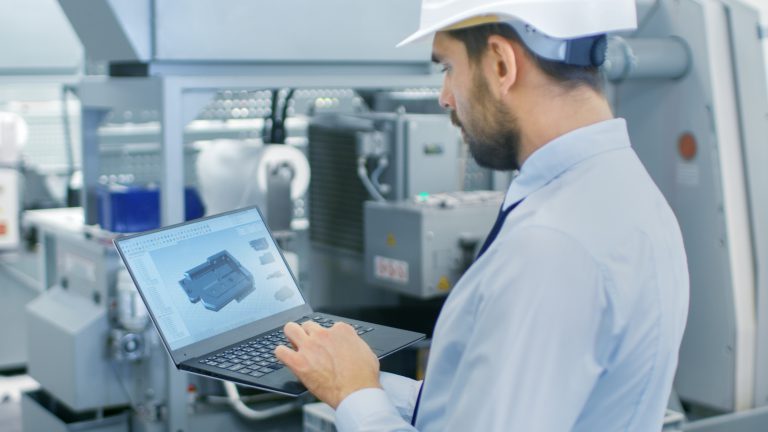
Transforming the Industry
Digital Transformation is a combination of traditional manufacturing processes enhanced with new advancing technologies, working together to drive manufacturing forward and address inefficiencies in the current sector.
Technology and software will have a huge role to play, integrating into all areas of the business transforming traditional processes to change how a business operates and deliver more value to customers.
Driven by technology, Industry 4.0 will transform production and reshape businesses, creating greater efficiency and better relationships between producers, suppliers and customers.
Global Data’s Disruptor Tech Database reveals that big data and analytics and additive manufacturing (3D printing) are amongst the technologies considered crucial in transforming industrial manufacturing.
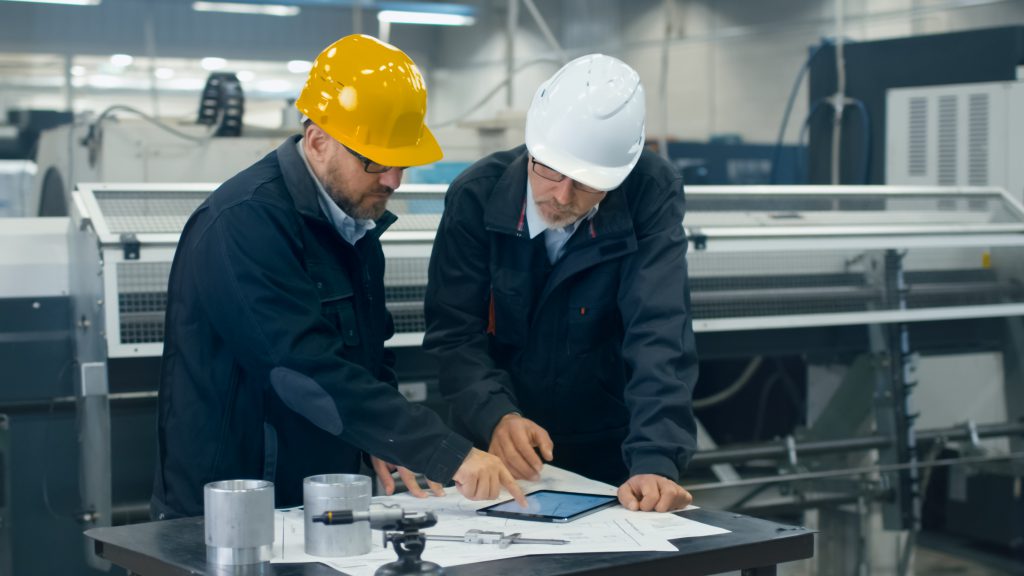
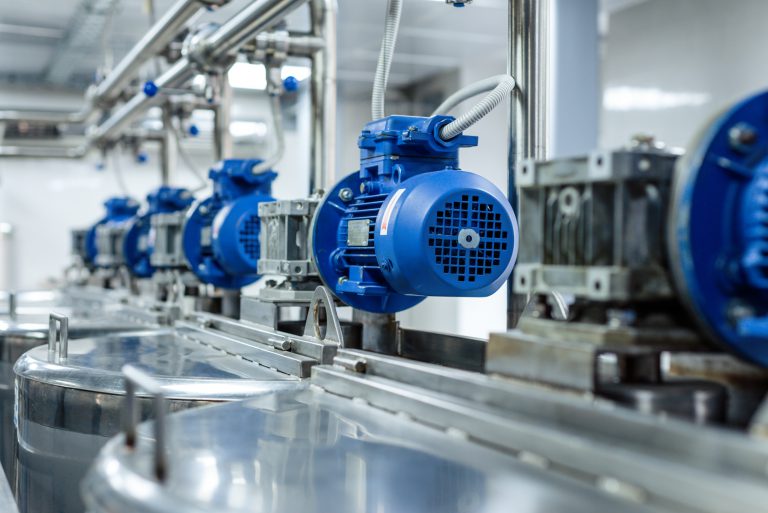
Smart Manufacturing
Powered by data and automation, digital transformation is transforming every step of the manufacturing process, from supply chain and enterprise to the shop floor and end users.
The National Institute of Standards and Technology describe Industry 4.0 as creating “fully integrated, collaborative manufacturing systems that respond in real time to meet changing demands and conditions in the factory, in the supply network and in customer needs.”
Smart manufacturing is connecting factories digitally, with central networks linking with machines, not only to automate but to learn processes independently, adapt to change, generate orders, understand quality issues and even assign tasks to other machines.
Deloitte Insights describes the smart factory as a leap forward from more traditional automation to a fully connected flexible system.
Connecting data, people and systems is key to smart manufacturing, making information available when and where it is needed, across the entire manufacturing process.
Manufacturing Tomorrow agrees that “by using sensors, robotics and a central collection of data, smart factories enable all information about the manufacturing process to be available across entire manufacturing supply chains and product lifecycles.“
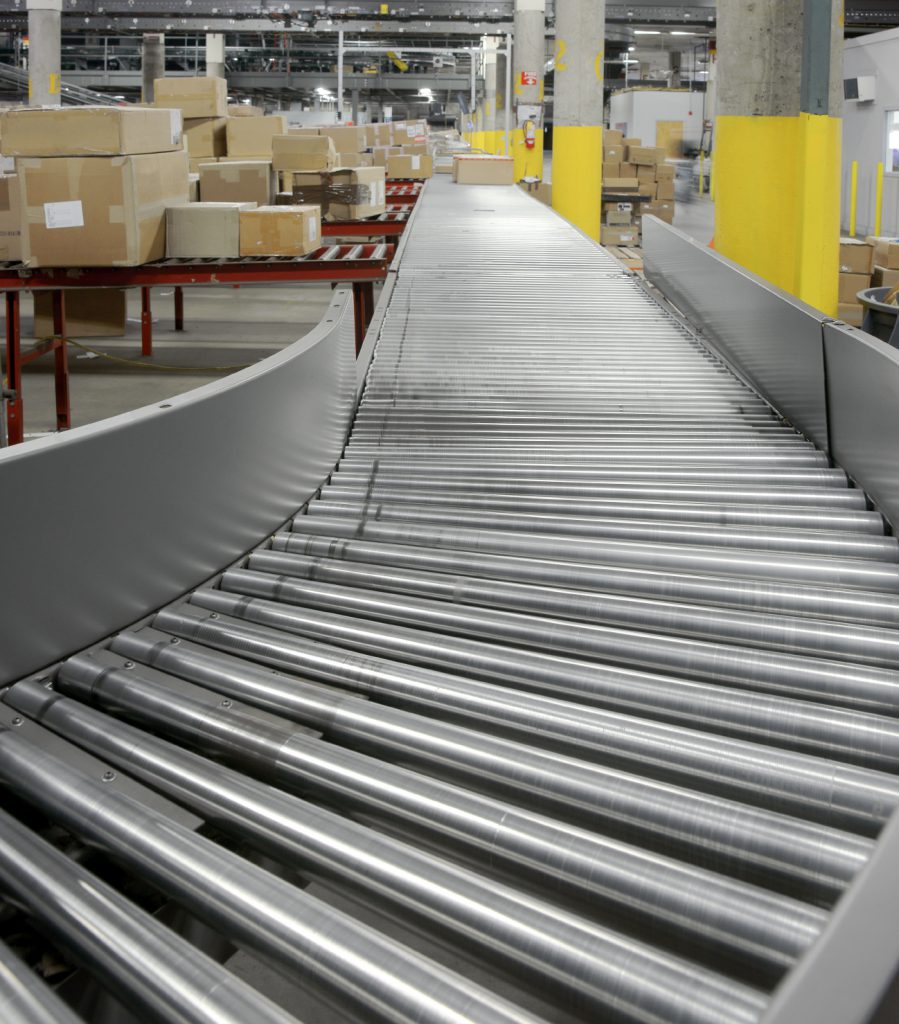
What Does This Mean For Manufacturers?
Smart manufacturing, mass customization, automation and lean manufacturing are disrupting the industry.
By adopting and implementing smart technologies, manufacturers are able to increase productivity, improve inefficiencies and create sustainability.
Smart manufacturing is all about increasing throughput, uptime and performance while reducing overhead costs, operating costs and capital costs.
Moving Forward
At DriveWorks, we recognise that smart manufacturing is the future that is changing the way manufacturers work.
Aerospace Defence Security describe the many benefits of a fourth industrial revolution as boosting productivity, increasing efficiency, improving quality and reducing waste across the entire value chain.
With the introduction of smart manufacturing and smart factories comes the importance of good data. Information is an asset to all businesses and is now powering digital transformation by enabling real-time, learning-based decision-making across all business operations, including product development, manufacturing, supply chain, and customer experience.
Manufacturers need to take inspiration from past industrial revolutions, embrace the change or risk being left behind and overtaken by competitors.
Change is scalable, with a few small changes manufacturers can improve their data, make better connections between systems and teams and make their business more digital, resulting in better customer experience.
As Industry 4.0 continues to evolve, there are many programmes and initiatives to help manufacturers and engineers to explore the opportunities and benefits of digitalisation and embrace Industry 4.0.
This is the first blog in our new digital transformation series. Each week we will be sharing our insights about the importance of embracing digital transformation and automation. Keep reading to learn more!