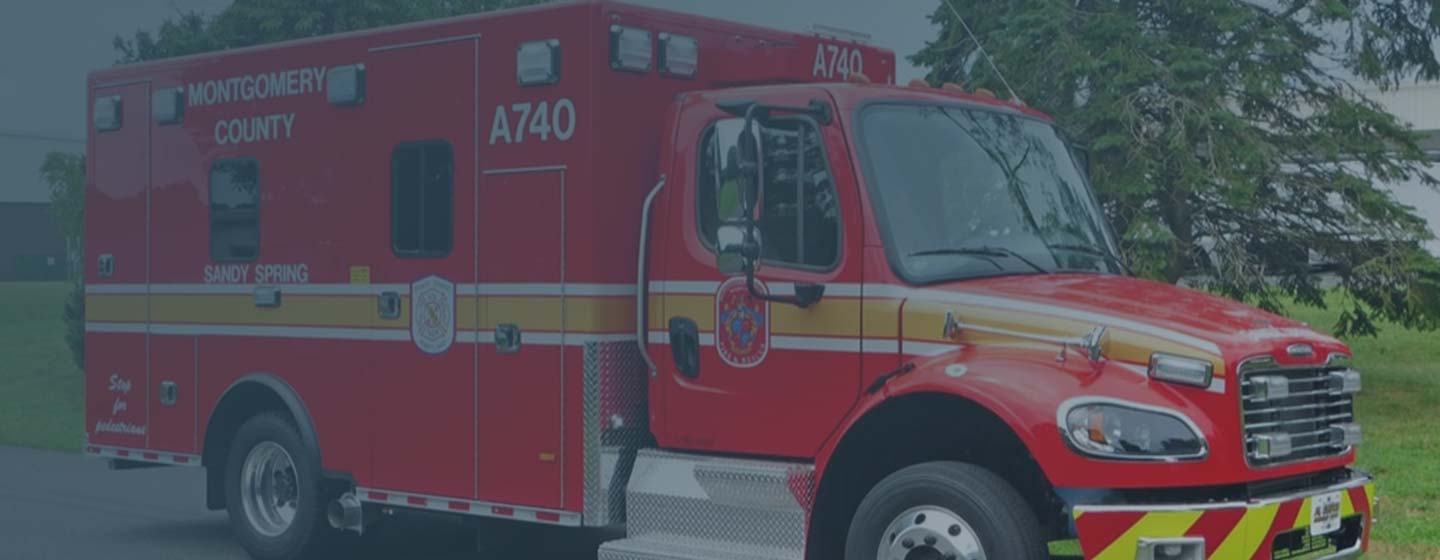
PL Custom
PL Custom free up engineers to focus on customized aspects of designs by automating repetitive SOLIDWORKS® modelling tasks
Challenge
PL Custom provide unique emergency vehicles tailored exactly to customer needs. They needed a solution to free up engineers from repetitive SOLIDWORKS modelling tasks, so they could focus on the custom aspects of vehicle designs.
Solution
Repetitive and time-consuming SOLIDWORKS modelling tasks have been automated using DriveWorks Pro. Engineering capacity has been increased, giving engineers more time to work on custom designs to solve customer challenges.
Results
DriveWorks handles repetitive modelling tasks and automatically outputs 245 files, consisting of 60 assemblies, 85 drawings and 100 parts files. This has freed engineers up to focus on the customized aspects of their designs, such as custom internal cabinetry.
Company overview
PL Custom are a custom vehicle manufacturer supplying type 1 and type 3 ambulances, as well as custom rescue trucks. They were founded in 1946 and are based in Manasquan, NJ. PL Custom are represented throughout the USA by 17 dealers, covering 29 states and 1 dealer covering parts of Canada.
They have approximately 185 members of staff, 97 of whom work in production, 26 in sales and the rest are engineers, admin and internal sales.
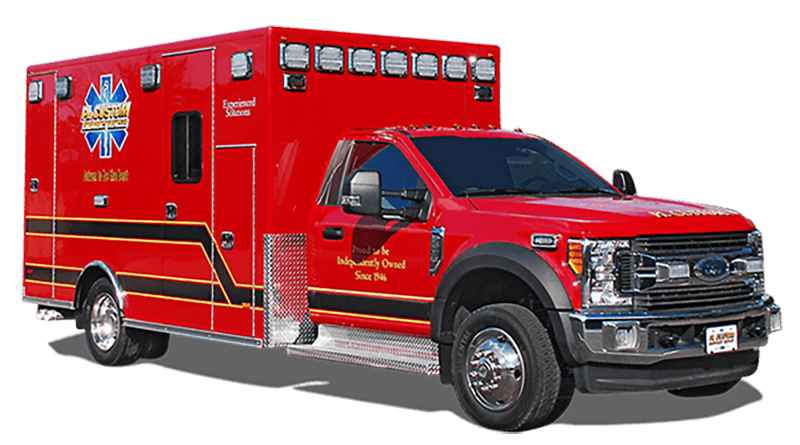
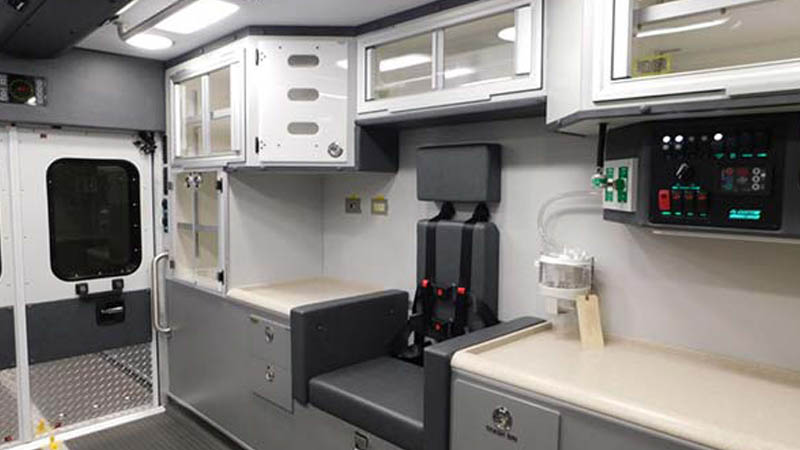
Challenge
Focus engineers on custom aspects of designs
PL Custom wanted their engineers to focus on the custom aspects of their designs and not the configurable options. With hundreds of standard configurable options available, they needed a solution to automate repetitive, time-consuming modelling tasks and free up engineers.
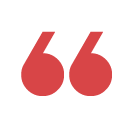
With DriveWorks handling repetitive tasks, our engineers are freed up to focus on the customized aspects of our designs – such as the internal cabinets of the vehicle
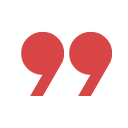
Shawn Casebolt – Engineering Lead
PL Custom
Solution
Design automation for SOLIDWORKS
PL Custom were already using SOLIDWORKS 3D CAD so they turned to DriveWorks for their design automation solution.
When asked about how PL Custom approached the implementation of DriveWorks, Shawn Casebolt, Engineering Lead explained
“We started by laying out what we thought we wanted our model structure to consist of. This was then revised and it continues to be revised as we further develop it.”
“We decided that we’d pick our most popular model and begin with the basic exterior frame. Then we’d bring more models into the mix based upon their popularity. Once we achieved around 80% of our models (by sales) then we would move on to content.”
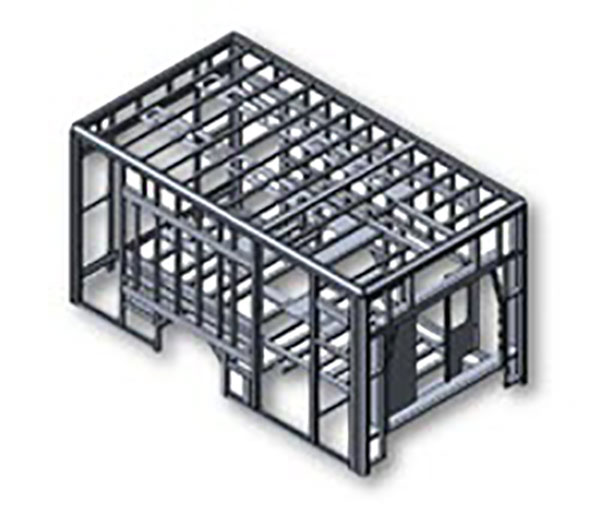
Results
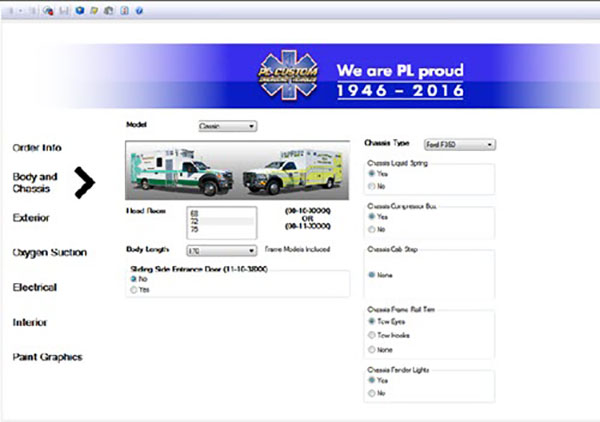
Reducing repetitive engineering tasks
PL Custom have successfully deployed DriveWorks and are already seeing the benefits of reducing repetitive engineering tasks.
Engineers input the vehicle specification into custom designed forms, built using the intuitive DriveWorks form designer. 2D and 3D visual previews provide the engineers with immediate feedback of their selections and ensure the configured vehicle matches the customer contract.
Compartment sizes, as well as the body length and height are used by DriveWorks to automatically configure the weldment frame and exterior skins. PL Custom’s unique proprietary extrusions created as weldments in SOLIDWORKS are automatically selected by DriveWorks based on the vehicle configuration. PL Custom are also using DriveWorks to automatically drive their most popular lighting selections and combinations.
Maintaining consistency is simple
Shawn explains “even small parts, such as door trims, have their own assembly and drawing. But this is simple as DriveWorks is consistent with numbering and allows us to drive the lengths based on door heights. Compartments, like most other items, also have their own sub-assembly. These fit into the door openings that DriveWorks is generating in the frames.”
“In its current state, DriveWorks outputs 245 files, 60 of which are assemblies, 85 are drawings and the rest are parts files. With DriveWorks handling these repetitive tasks, our engineers are freed up to focus on the customized aspects of our designs – such as the internal cabinets of the vehicle.”
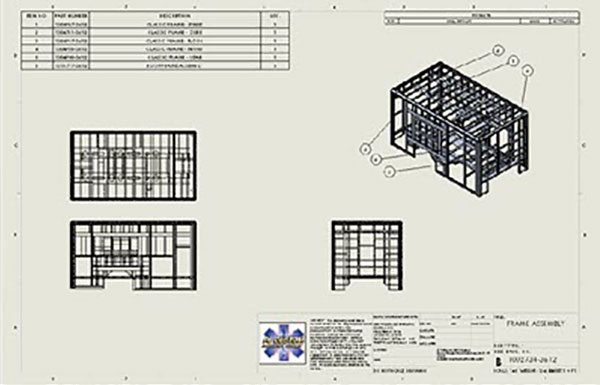
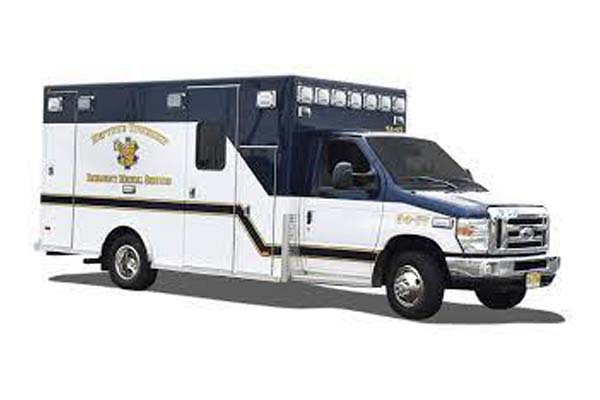
Future
“Our primary focus is to increase our content level and our ability for interference detection and to drive purchasing. This will include adding the cots, attendant seats, doors and metal inserts for the cabinets. In the long term future, we will focus on the exterior of the vehicles and all lights, bumpers and other items.”
“We would like to eventually transition driving all purchasing from our models and being able to utilize DriveWorks for quoting projects.”
Shawn Casebolt – Engineering Lead
Try DriveWorks Pro configurator examples online
Request a demo with a technical specialist
Fill out the form below and a member of the DriveWorks team will be in touch.